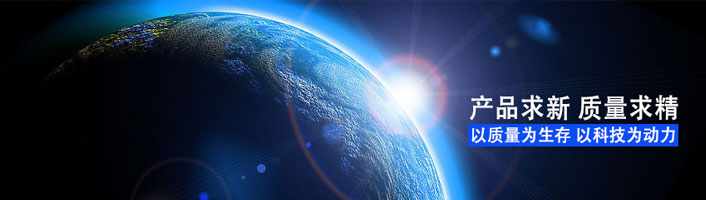
振动监测参数选择与判定标准
机械运动消耗的能量除了做有用功外,其他的能量消耗在机械传动的各种摩擦损耗之中,并产生正常振动。如果出现非正常的振动,说明机械发生故障。这些振动信号包含机械内部运动部件各种变化信息。分辨正常振动和非正常振动,采集振动参数,运用信号处理技术,提取特征信息,判断机械运行的技术状态,这就是振动检测。
在机械设备的振动监测中,往往是将测得的振动参数量值与判断标准进行对比,从而分析判定振动的原因和机器状态的好坏.目前,在现场实际应用中,主要是参照国际标准ISO、某些国外先进标准、我国的部标、专业标准,或结合本行业设备具体情况制定限值来进行分析判定.
(1)振动测量的方位选择
① 测量位置(测点)
测量的位置选择在振动的敏感点,传感器安装方便,对振动信号干扰小的位置,如轴承的附近部位。
② 测量方向
由于不同的故障引起的振动方向不同,一般测量互相垂直的三个方向的振动,即轴向(A向)、径向(H向、水平方向)和垂直方向(V向)。例如对中不良引起轴向振动;转子不平衡引起径向振动;机座松动引起垂直方向振动。高频或随机振动测量径向,而低频振动要测量三个方向。总之测量方向和数量应全面描述设备的振动状态。
(2)测量参数的选择
测量振动可用位移、速度和加速度三个参数表述。这三个参量代表了不同类型振动的特点,对不同类型振动的敏感性也不同。
① 振动位移
选择使用在低频段的振动测量(<10Hz),振动位移传感器对低频段的振动灵敏。在低频段的振动,振动速度较小,可能振动位移很大,如果振动产生的应力超过材料的许用应力,就可能发生破坏性的故障。
② 振动速度
选择使用在中频段的振动测量(10~1000Hz)。在大多数情况下转动机械零件所承受的附加载荷是循环载荷,零件的主要失效形式是疲劳破坏,疲劳强度的寿命取决于受力变形和循环速度,即和振动位移与频率有关,振动速度又是这两个参数的函数,振动能量与振动速度的平方成正比。所以将振动速度作为衡量振动严重程度的主要指标。
③ 振动加速度
选择使用在高频段的振动测量(>1000Hz)。当振动频率大于1000Hz时,动载荷表现为冲击载荷,冲击动能转化为应变能,使材料发生脆性破坏。多用于滚动轴承的检测。
以上这三个参量可以互为辅助性的补充和参考。
(3)振动判定标准
① 绝对判断标准
此类标准是对某类机器长期使用、维修、测试的经验总结,由行业协会或国家制定图表形式的标准。使用时测出的振动值与相同部位的判断标准的数值相比较来做出判断。一般这类标准是针对某些类型重要回转机械而制定的。
例如国际通用标准ISO2372 和 ISO3945。
② 相对判断标准
对同一设备的同一部位定期进行检测,按时间先后做出比较,以初始的正常值为标准,以后实测振动值超过正常值的多少来判断。
③ 类比判断标准
在相同工作条件下,多台相同规格的运行设备,对各台设备的同一部位进行振动测量,根据结果判断,如果某台设备的振动值超过其余设备的振动值一倍以上,视为异常。此方法是在无标准可参考的情况下采用。
以上的各种判断标准要根据不同设备、不同使用条件、不同的环境选择合适的标准。还要以总结实践经验和参照维修数据进行分析,丰富和修正使用的标准。
④ 振动判断的显示
一般采用统一的颜色来表示设备的运行振动状态。
深绿色--良好;
浅绿色--合格;
浅红色--容许值;
深红色--劣化状态。
任何机械在输入能量转化为有用功的过程中,均会产生振动。振动的强弱与变化和故障相关,非正常的振动增强表明故障趋于严重。不同的故障引起的振动特征各异,相同的振动特征可能是不同的故障。振动信号是在机器运转过程中产生的,就可以在不用停机的情况下检测和分析故障。
相关推荐:
下一篇:建立设备
-
设备状态监测管理系统
-
设备点检管理系统
-
安卓无线点检仪
-
安卓无线测振仪
-
传感单元