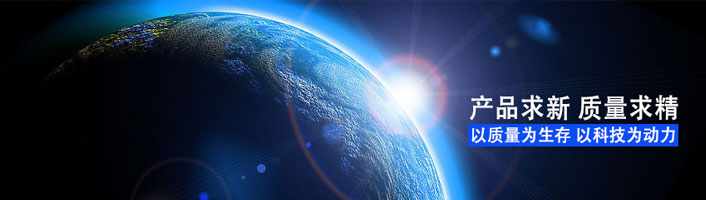
状态监测与智能诊断系统——设备体检好医生
随着物联网的发展,数据传输资费正在不断降低,无线通信的成本在逐年减少,而依靠无线网络进行数据传输的监控行业的远程监控成本大大下降,让工控无线监控行业得以快速发展。无线监控系统可以实现无线远程监测和控制,无需人工监测和人工操作,节省大量的人力、物力,极大地提高安全系数。故障智能诊断,以往通过人工点检方式巡查,虽然已经具备振动和温度的测量和诊断分析数据,但是点检员或技术员不具备专业的振动分析理论基础,读取图谱能力有限,无法根据振动图谱进行故障分析。
系统可实现目标
(1) 实时监测与报警:泵站各项监控参数、振动温度参数的实时监测,报警;
(2) 远程启停控制:远程控制泵站启停。
(3) 健康状态综合评估:机泵健康状态评估,并给出评估报高。
(4) 故障诊断:健康状态不良时,给出故障部位和故障原因,并提交诊断报告和维修建议。
(5) 缺陷处理:故障确认后,进入维修流程,记录维修记录,保存典型案例。
主要功能
(1) 设备档案:设备基础信息、维修记录、监测日志等信息存储与查询;
(2) 参数设置:设置监测测点、振动采集与分析参数、报警值设置、故障特征指标设置、频带能量设置等;
(3) 在线管理:设置监测测点、监测参量及其报警值设置、故障特征指标设置、频带能量设置等;
(4) 状态报警:可运行数据实时显示,运行数据、振动及其特征值、温度的趋势图以及当前状态;
(5) 运行控制:跟踪设备运行状态,报警后发送消息到技术手机,可通过远程中心电脑端、手机端或本地控制台对机泵进行开停控制;
(6) 故障跟踪:设置不同故障的敏感指标,监测其数值变化实现故障跟踪定位;
(7) 精密诊断:可实现振动波形分析、频谱分析、包络谱图、瀑布图、色谱图等故障诊断图谱,用于设备精密故障分析;
(8) 诊断报告:生成故障和诊断报告,含设备基础信息、故障特征值、振动总值、报警状态、波形图、频谱图等;
(9) 故障案例:根据历史诊断和检修情况,为典型故障录入故障案例,为日后故障诊断分析提供参考;
(10) 统计报表:报警次数统计、不同报警等级的设备数量统计、运行或停机设备数量统计;
(11) 用户权限:不同用户设置不同的权限范围,以不同帐号和密码登录;
(12) 微信推送:关注微信公众号,订阅需要的状态信息或报表,系统自动通过微信发送个相关人员的微信号。及时了解设备当前状态,避免遗漏重大问题。
状态监测项目的立项是在充分考虑不同产线设备特点,结合工艺要求及现场环境的基础上进行论证的,针对铁前区域、钢轧区域分别采取了无线方案和有线方案两种方式,即无线采集+有线传输、有线采集+有线传输,通过传感器采集机组径向或轴向的振动加速度、速度、温度等信号,实现每个测点的振动、温度趋势变化监测;通过监测关键设备运行时主传动链(电机/汽机、齿轮箱)系统上各轴、轴承、齿轮的运行状态,能够发现轴承、齿轮箱及电机故障的早期征兆,精确定位故障部件、故障类型以及严重程度,在此基础上,结合数采系统,还将部分生产工艺信号导入在线监测系统,做为辅助分析设备隐患及故障的重要依据。
除了分布式架构设计外,此系统具备丰富的数据分析功能,支持多种诊断工具,如时域波形、频谱、包络解调、瀑布图、多频谱等多种分析方法;具备分析振动的原始、趋势数据的功能,并能够将多组、多点数据进行比较分析。可根据机组运行模式,对振幅、有效值、峰峰值、翘度、通频值等指标进行历史趋势分析。具备报警参数设置功能,可按多种方式设置报警;同时,系统提供了自动的特征频率计算,可根据结构参数计算出轴承、电机、叶轮等多种零部件的特征频率;能够对硬件系统的网络通信状态、传感网络状态及内部硬件信息等进行自检;最终通过数据分析,判定机组故障程度、故障原因、故障部位,提出检修建议, 确定寿命预期;同时,支持多类型数据采集策略,如同步振动采集、转速采集、基于转速触发的振动数据采集以及异常状态下的加密采集,避免故障数据的遗漏;同时还具备手机APP功能,能够实时查看设备状态和接受报警信息。
随着大数据挖掘技术的发展,设备运行状态的远程监测与精密故障诊断得到了数据和技术支撑,为设备故障预测和维修提供了更加有利的条件。远程监测和智能诊断模块通过监测机泵的振动、温度、电流、电压、转速以及控制系统的各项运行参数,模块自动读取振动图谱中的故障特征指标,结合控制系统的参数一并,采用多参量多指标等多元统计分析技术,实现设备运行的健康监测和故障诊断。
相关推荐:
-
设备状态监测管理系统
-
设备点检管理系统
-
安卓无线点检仪
-
安卓无线测振仪
-
传感单元